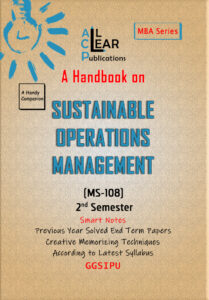
- Topic (1)-Nature and Scope of Operations Management
- Definition of Operations Management
- Historical background and development of Operations Management
- Scope of Operations Management
- Importance of Operations Management in businesses
- Topic (2)-Historical Evolution of Operations Management
- Scientific Management and its influence on Operations Management
- Development of Operations Management during the Industrial Revolution
- Contributions of key individuals to Operations Management
- Topic (3)-System Perspectives of Operations Management
- Overview of systems theory and its application to Operations Management
- Components of a system
- Examples of systems in Operations Management
- Topic (4)-Relationship of Operations Management with Other Functional Areas
- Overview of the functions of an organization
- Interactions between Operations Management and other functional areas
- Importance of coordination and communication between functions
- Topic (5)-Operation Strategy
- Topic (6)-Recent Trends in the Field of Operations Management
- Overview of recent developments in Operations Management
- Examples of new technologies and innovations in Operations Management
- Topic (7)-Sustainability in Operations
- Definition of sustainability and its importance in Operations Management
- Examples of sustainable practices in Operations Management
- Challenges and benefits of implementing sustainable practices in Operations Management
- Topic (8)-Ecological Considerations by Manufacturing and Services Firms
Topic (1)-Nature and Scope of Operations Management
Definition of Operations Management
Operations management is the process of planning, organizing, coordinating, and controlling all the activities involved in creating goods and services. It is a multidisciplinary field that involves the design, management, and improvement of processes and systems that transform inputs into outputs. Operations management is concerned with ensuring that organizations are able to meet the needs of their customers efficiently and effectively, while also minimizing costs and maximizing quality.
Historical background and development of Operations Management
The field of operations management has evolved over time in response to changes in technology, economics, and business practices. Some of the key milestones in the development of operations management include:
(1) Industrial Revolution: The Industrial Revolution, which began in the late 18th century, brought about significant changes in the way goods were produced. The introduction of new technologies such as the steam engine and the power loom led to the development of large-scale factories, and the need for more systematic approaches to production.
(2) Scientific Management: In the early 20th century, Frederick Taylor introduced the principles of scientific management, which focused on improving efficiency by analyzing and optimizing work processes.
(3) Fordism: In the 1910s and 1920s, Henry Ford introduced the concept of Fordism, which involved the mass production of standardized goods using assembly line techniques.
(4) World War II: The demands of World War II led to significant advancements in the field of operations management, including the development of mathematical models for optimization and the use of statistical quality control.
(5) Lean Manufacturing: In the 1950s, Toyota introduced the principles of lean manufacturing, which emphasized the elimination of waste and the continuous improvement of processes.
(6) Total Quality Management: In the 1980s and 1990s, the concept of total quality management became popular, which emphasized the importance of customer satisfaction, employee involvement, and continuous improvement.
Scope of Operations Management
The scope of operations management encompasses the planning, designing, and control of the production process to ensure that the products and services meet customer demands while maximizing efficiency and minimizing costs. It includes various aspects such as:
(1) Product design: Operations management plays a crucial role in product design, which involves developing new products that meet customer needs and preferences. It involves analyzing customer needs, identifying the features and characteristics of the product, and developing a prototype that meets the customer’s needs.
(2) Process design: Once the product design is complete, operations management focuses on designing the production process. This involves selecting the equipment, machines, and tools necessary for the production process and designing the layout of the production facility.
(3) Capacity planning: Operations management involves determining the capacity of the production process to meet customer demand. It includes analyzing the demand for the product, the production capacity of the facility, and the availability of resources.
(4) Production planning and control: Operations management involves planning and controlling the production process to ensure that the products are manufactured efficiently and meet customer demand. This includes developing a production schedule, monitoring the production process, and controlling the inventory of raw materials and finished goods.
(5) Quality control: Operations management plays a critical role in ensuring the quality of the products and services. It includes monitoring the production process to detect defects and identifying the root cause of the defects. It also involves developing quality control procedures to ensure that the products meet the desired quality standards.
(6) Supply chain management: Operations management involves managing the entire supply chain, including suppliers, manufacturers, distributors, and retailers. It involves coordinating the flow of goods and services from the suppliers to the customers, minimizing costs, and maximizing efficiency.
Importance of Operations Management in businesses
Operations Management is of immense importance to businesses for the following reasons:
(1) Improves Efficiency: Operations Management helps in improving the efficiency of the business processes. By analyzing and optimizing processes, businesses can reduce wastage, improve productivity, and reduce costs, resulting in increased profits.
(2) Enhances Quality: Operations Management plays a critical role in ensuring high quality of products or services. By implementing quality control measures and continuously improving processes, businesses can deliver consistent quality products or services, resulting in higher customer satisfaction and loyalty.
(3) Increases Customer Satisfaction: Effective Operations Management leads to better customer satisfaction by delivering the right products or services on time, at a reasonable cost and with good quality. Customer satisfaction leads to repeat business, referrals and a good reputation in the market.
(4) Facilitates Innovation: Operations Management facilitates innovation by constantly seeking to improve and optimize business processes. By adopting new technology, materials and methods, businesses can develop new and better products, and services, and stay ahead of the competition.
(5) Helps in Decision Making: Operations Management provides managers with the information and tools needed to make informed decisions. By analyzing data and using various techniques, such as forecasting, capacity planning, and inventory management, managers can make better decisions and minimize risks.
(6) Enables Growth: Operations Management helps businesses to grow and expand. By optimizing processes and increasing efficiency, businesses can handle higher volumes of production, expand into new markets and regions, and diversify their product or service offerings.
Topic (2)-Historical Evolution of Operations Management
Scientific Management and its influence on Operations Management
Scientific Management, also known as Taylorism, is a management theory developed by Frederick Winslow Taylor in the late 19th century. The theory aims to optimize and standardize work processes by breaking down each task into its component parts and analyzing each part to find the most efficient way of performing the task. This approach has had a significant influence on the development of Operations Management. Taylor’s ideas about work measurement, work analysis, and standardization of work processes have been the foundation for many contemporary concepts in Operations Management, including time and motion study, job design, and work simplification.
Development of Operations Management during the Industrial Revolution
The Industrial Revolution was a period of rapid industrialization that occurred in the late 18th and early 19th centuries. During this period, many manufacturing processes were mechanized, leading to the creation of large-scale factories. This development led to the emergence of Operations Management as a distinct discipline. The goal was to optimize the manufacturing process, reduce costs, and increase productivity. Key concepts developed during this period include mass production, standardization, and division of labor.
Contributions of key individuals to Operations Management
(1) Eli Whitney: Eli Whitney is known for inventing the cotton gin, which revolutionized the cotton industry in the United States. However, he also contributed to the development of Operations Management by introducing the concept of interchangeable parts. This idea made it possible to manufacture products in large quantities and led to the development of mass production.
(2) Henry Ford: Henry Ford is known for revolutionizing the automotive industry with his innovative approach to mass production. He introduced the assembly line, which allowed for the rapid and efficient production of automobiles. His ideas about standardization and production efficiency have had a lasting impact on Operations Management.
(3) Taiichi Ohno: Taiichi Ohno is considered the father of the Toyota Production System, which is the basis for lean manufacturing. He developed many of the core principles of the system, including just-in-time production, continuous improvement, and waste reduction. His ideas have had a significant impact on Operations Management, particularly in the area of process improvement.
Topic (3)-System Perspectives of Operations Management
Overview of systems theory and its application to Operations Management
Systems theory is an interdisciplinary approach to understanding complex systems that are made up of numerous interconnected elements. It has been used in a variety of fields, including engineering, biology, sociology, and management, to study complex systems and identify ways to optimize their performance. In the field of Operations Management, systems theory provides a framework for understanding the processes, inputs, and outputs of an organization’s operations.
The application of systems theory to Operations Management is based on the idea that every operation can be understood as a system with inputs, processes, and outputs. The inputs are the resources that are required for the operation, such as raw materials, equipment, and labor. The processes are the steps that are taken to transform these inputs into finished goods or services, and the outputs are the end products that are delivered to customers.
The following are some of the key concepts of systems theory and their application to Operations Management:
(1) Interconnectedness: Systems theory emphasizes that all elements of a system are interconnected, and changes in one part of the system can have a ripple effect throughout the entire system. In the context of Operations Management, this means that decisions made in one area of the operation can affect other areas and the overall performance of the system.
(2) Feedback loops: Systems theory emphasizes the importance of feedback loops, which allow a system to self-regulate and adjust to changes in the environment. In the context of Operations Management, feedback loops can be used to monitor the performance of the operation and identify areas for improvement.
(3) Boundary management: Systems theory emphasizes the importance of managing the boundaries of a system, which define what is included within the system and what is outside of it. In the context of Operations Management, this means defining the scope of the operation and the interfaces with other departments or organizations.
(4) Subsystems: Systems theory recognizes that a system can be divided into subsystems, which are smaller systems that are interconnected and interdependent. In the context of Operations Management, subsystems can be used to focus on specific areas of the operation, such as quality control or supply chain management.
(5) Optimization: Systems theory provides a framework for optimizing the performance of a system, by identifying the inputs and processes that are most effective at achieving the desired outputs. In the context of Operations Management, this means identifying the most efficient and effective ways to transform inputs into finished goods or services.
Components of a system
A system is an interdependent set of components that work together to achieve a common goal. The components of a system can be classified into four categories: inputs, processes, outputs, and feedback. These components are interrelated and work together to achieve the system’s objectives.
(1) Inputs: Inputs refer to the resources that are necessary to create the system’s output. Inputs can take different forms, such as raw materials, information, energy, or equipment. Inputs are transformed by the system’s processes to produce the system’s output.
(2) Processes: Processes refer to the activities that transform inputs into outputs. Processes can take different forms depending on the nature of the system. For example, a manufacturing system’s processes might include designing a product, sourcing raw materials, assembling the product, and testing the final product. In contrast, a service system’s processes might include customer service, invoicing, and order fulfillment.
(3) Outputs: Outputs refer to the products, services, or information that are generated by the system’s processes. Outputs can take different forms, such as a physical product, a report, or a service. The quality and quantity of the output are influenced by the quality and quantity of the inputs and the effectiveness of the processes.
(4) Feedback: Feedback refers to the information that is generated by the system’s output and is used to modify the system’s processes or inputs. Feedback can be either positive or negative. Positive feedback occurs when the output of the system reinforces the system’s processes or inputs. Negative feedback occurs when the output of the system causes the system’s processes or inputs to be modified to improve the system’s output.
Examples of systems in Operations Management
In operations management, systems are integral to the functioning of a business. Here are a few examples of systems in operations management:
(1) Supply chain system: A supply chain system is a set of interconnected entities that work together to move a product or service from the supplier to the customer. It involves processes such as sourcing, procurement, logistics, production, and delivery. The supply chain system ensures that products or services are delivered to customers in the most efficient way possible while meeting their requirements.
(2) Production process system: The production process system involves the steps required to convert raw materials into finished products. The system includes processes such as product design, process planning, production scheduling, quality control, and inventory management. The production process system aims to optimize the use of resources, reduce waste, and increase productivity.
(3) Quality management system: A quality management system is a set of processes and procedures that ensure that products or services meet or exceed customer expectations. The system includes processes such as quality planning, quality assurance, and quality control. The quality management system helps to ensure that products or services are consistently of high quality.
(4) Inventory management system: An inventory management system is a set of processes and procedures that govern the ordering, storing, and usage of inventory. The system includes processes such as forecasting, replenishment, and tracking. The inventory management system aims to optimize inventory levels, minimize stockouts, and reduce inventory costs.
(5) Information system: An information system is a set of processes and procedures that manage and disseminate information throughout an organization. The system includes processes such as data collection, analysis, and reporting. The information system helps to ensure that accurate and timely information is available to support decision-making.
These systems work together to enable businesses to operate efficiently and effectively. By understanding and managing these systems, operations managers can optimize business processes and increase profitability.
Topic (4)-Relationship of Operations Management with Other Functional Areas
Overview of the functions of an organization
An organization can be viewed as a system of various interconnected parts or functions that work together to achieve a common goal or purpose. The main functions of an organization include:
(1) Marketing: The marketing function is responsible for identifying customer needs and wants and developing products or services that satisfy those needs. Marketing also involves pricing, promoting, and distributing products or services to the target market.
(2) Finance: The finance function manages the financial resources of the organization, such as funds, investments, and debt. It is responsible for budgeting, financial planning, and financial reporting.
(3) Human Resources: The human resources function is responsible for managing the people within the organization. This includes recruitment, training, performance management, and employee relations.
(4) Operations: The operations function is responsible for producing goods or services that meet customer needs. This includes activities such as production planning, scheduling, inventory management, quality control, and process improvement.
(5) Information Technology: The information technology function manages the technology and systems used within the organization. This includes hardware, software, data management, and communication systems.
(6) Legal: The legal function ensures that the organization operates within the law and manages legal risks. This includes activities such as contract management, regulatory compliance, and dispute resolution.
(7) Administration: The administration function manages the day-to-day operations of the organization. This includes activities such as office management, facilities management, and record keeping.
Interactions between Operations Management and other functional areas
Operations Management (OM) is a functional area that has close interactions with other functional areas within an organization. These interactions are critical to achieving overall organizational goals and objectives. Some of the functional areas that have a direct impact on OM are:
(1) Marketing: Marketing provides input to operations management regarding the expected demand for a product or service. OM uses this information to plan and schedule production activities to ensure that there is enough capacity to meet the expected demand.
(2) Finance: Finance plays a crucial role in providing resources for the organization’s operations. OM works with finance to develop budgets and financial plans for production activities. OM also uses financial information to evaluate the performance of production activities and make necessary adjustments.
(3) Human Resources: Human resources provide the necessary labor for production activities. OM works closely with HR to determine the skills and expertise required for different production activities. OM is also involved in developing training programs for the workforce to ensure that they have the necessary skills to perform their duties.
(4) Information Technology: Information technology has become an integral part of operations management. OM uses technology to manage the production process, monitor performance, and track inventory. OM also uses technology to communicate with suppliers and customers to ensure that the supply chain is efficient.
(5) Research and Development: Research and development play a critical role in the development of new products and processes. OM works closely with R&D to ensure that the new products or processes can be manufactured efficiently and cost-effectively.
Importance of coordination and communication between functions
Effective coordination and communication between functions is essential for the success of an organization. Without proper communication and coordination, different functional areas may work in silos, resulting in conflicts and inefficiencies.
One of the key reasons why coordination and communication between functions are important is that most business processes are interconnected and interdependent. For instance, the operations function is responsible for producing goods or services, while the marketing function is responsible for promoting them. If these two functions do not coordinate with each other, the marketing function may create demand for products that the operations function cannot produce, resulting in stockouts and dissatisfied customers.
Similarly, the finance function is responsible for managing the financial resources of the organization, and it must coordinate with the operations function to ensure that adequate funds are available to support production. If the two functions do not communicate properly, the organization may face a cash crunch, leading to delays in production and fulfillment of orders.
Coordination and communication between functions are also important for resource allocation. Each functional area has its own resource needs, and without proper coordination, there may be conflicts over resource allocation. For example, if the marketing function spends too much on advertising, there may be inadequate funds available for the operations function to purchase raw materials or equipment.
Topic (5)-Operation Strategy
Definition of Operation Strategy
Operations strategy refers to the process of designing and managing the operational processes and resources necessary to achieve organizational objectives. It involves developing a plan that outlines how a company’s resources, such as people, equipment, and technology, will be utilized to support the company’s mission and goals. Operations strategy is closely linked with business strategy, which involves defining the direction and scope of the organization, and making decisions on allocating resources to pursue this strategy.
Importance of Operation Strategy
Importance of Operations Strategy in achieving business goals:
(1) Alignment of operations with business goals: Operations strategy provides a framework for aligning the organization’s operations with its overall business strategy. It ensures that the operational processes and resources are working towards the same goals as the rest of the organization.
(2) Competitive advantage: An effective operations strategy can provide a competitive advantage to a business. By optimizing operational processes, a company can reduce costs, increase efficiency, and improve quality, thereby enhancing its competitiveness in the market.
(3) Resource utilization: Operations strategy is essential for ensuring that a company’s resources are being used efficiently and effectively. This includes the use of technology, labor, and materials, and optimizing the flow of work through the organization.
(4) Flexibility: Operations strategy provides a framework for managing change in the organization. By designing operational processes that are flexible and adaptable, companies can respond quickly to changes in the market and remain competitive.
(5) Customer satisfaction: Operations strategy is crucial for meeting customer expectations. By aligning operational processes with customer needs, companies can deliver products and services that meet or exceed customer expectations.
(6) Innovation: Operations strategy can drive innovation in the organization. By developing new and innovative ways to manage operations, companies can create new products and services, improve quality, and increase efficiency.
(7) Long-term planning: Operations strategy is critical for long-term planning. It involves developing plans and processes that can be sustained over the long term, ensuring that the organization is well-positioned to achieve its goals and objectives.
Types of Operation Strategy
Types of Operation Strategy:
(1) Low-cost strategy: Companies pursuing a low-cost strategy focus on reducing the cost of production and minimizing expenses without sacrificing quality. This strategy is typically used by companies that compete in price-sensitive markets where customers are looking for low-cost alternatives. To achieve this, companies may implement cost-cutting measures in areas such as production, supply chain management, and inventory control.
(2) Differentiation strategy: Companies pursuing a differentiation strategy focus on providing unique and high-quality products or services that stand out from their competitors. This strategy is typically used by companies that compete in markets where customers value quality, uniqueness, and innovation. To achieve this, companies may invest heavily in research and development, marketing, and branding.
(3) Focus strategy: Companies pursuing a focus strategy focus on serving a specific segment of the market. This strategy is typically used by companies that have identified a particular customer group or market niche and are looking to meet their specific needs. To achieve this, companies may develop specialized products or services, tailor their marketing efforts to the specific segment, and build relationships with key customers.
Each of these strategies requires a different approach to operations management. A low-cost strategy, for example, requires a strong focus on cost reduction and efficiency. This may involve reducing waste, optimizing production processes, and minimizing inventory levels. A differentiation strategy, on the other hand, requires a strong focus on product innovation, quality control, and branding. This may involve investing in research and development, building strong relationships with suppliers, and providing excellent customer service.
A focus strategy requires a strong focus on understanding the needs and preferences of a specific customer group. This may involve conducting market research, developing specialized products or services, and building relationships with key customers. Operations managers in companies pursuing a focus strategy need to be able to tailor their operations to the specific needs of the target market.
Topic (6)-Recent Trends in the Field of Operations Management
Overview of recent developments in Operations Management
In recent years, Operations Management has undergone significant changes and developments that have impacted the way businesses operate. Some of the recent developments in Operations Management are:
(1) Emphasis on Sustainability: One of the most significant recent developments in Operations Management is the increased emphasis on sustainability. Organizations are becoming more aware of their impact on the environment and society and are taking steps to reduce their carbon footprint, conserve natural resources, and promote social responsibility.
(2) Advancements in Technology: Advancements in technology have greatly impacted Operations Management. New technologies such as the Internet of Things (IoT), Artificial Intelligence (AI), and Robotics have transformed manufacturing processes, supply chain management, and logistics. Automation and digitization have led to more efficient and cost-effective operations.
(3) Globalization: Globalization has led to a more interconnected world where companies can source raw materials, manufacture products, and sell goods and services on a global scale. This has created new opportunities for businesses, but it has also presented challenges such as managing complex supply chains and dealing with cultural and legal differences.
(4) Lean and Agile Operations: Lean and agile operations have gained popularity in recent years as organizations strive to become more flexible and responsive to changing customer demands. Lean operations focus on eliminating waste and reducing lead times, while agile operations emphasize adaptability and quick response to changing market conditions.
(5) Integration of Services and Products: Increasingly, companies are integrating services and products to create a more complete customer experience. This has led to the development of new business models, such as servitization, where companies sell services along with their products.
(6) Demand for Customization: Customers are increasingly demanding customized products and services, which has led to the rise of mass customization. Operations Management has responded to this demand by developing new strategies to produce customized products and services at scale.
(7) Supply Chain Risk Management: Supply chain risk management has become a critical concern for companies as supply chains become more complex and global. Natural disasters, political instability, and other disruptions can cause significant disruptions to supply chains, making risk management an important part of Operations Management.
(8) Focus on Quality: Quality has always been a key concern in Operations Management, but recent developments have placed even more emphasis on quality. Companies are increasingly adopting Total Quality Management (TQM) and other quality management approaches to ensure high-quality products and services.
Examples of new technologies and innovations in Operations Management
Operations management has seen a significant shift in recent years due to technological advancements and innovations. The development of new technologies has brought a wave of change that has transformed the way businesses operate. This section will focus on some examples of new technologies and innovations in Operations Management.
(1) Automation: Automation involves the use of technology to perform tasks that were previously done by humans. It is increasingly being used in manufacturing and production processes to increase efficiency and productivity. Automation can be seen in the form of robots and other advanced machinery that can perform repetitive tasks, handle heavy loads, and work for extended periods without rest. It can lead to increased efficiency, lower costs, and better quality control.
(2) 3D Printing: 3D printing is a form of additive manufacturing that involves the creation of three-dimensional objects by layering materials. It is being used in the production of a wide range of items, from car parts to medical implants. 3D printing offers many benefits, including reduced costs, faster prototyping, and the ability to create complex geometries that would be difficult or impossible to achieve using traditional manufacturing techniques.
(3) Artificial Intelligence (AI): AI is the simulation of human intelligence in machines that are programmed to learn and perform tasks that would normally require human intelligence. AI is being used in a variety of areas, including supply chain management, quality control, and demand forecasting. It can help to identify patterns and trends, automate repetitive tasks, and improve decision-making.
(4) Internet of Things (IoT): IoT refers to the interconnectedness of physical devices that are embedded with sensors, software, and other technologies, enabling them to collect and exchange data. IoT is being used in operations management to improve monitoring, tracking, and visibility across the supply chain. It can help to optimize inventory levels, reduce waste, and improve the accuracy of demand forecasting.
(5) Cloud Computing: Cloud computing involves the delivery of computing services over the internet, rather than on local servers. It is being used in operations management to enable businesses to store and access data remotely. Cloud computing can help to reduce costs, increase flexibility, and provide real-time access to critical information.
(6) Augmented Reality (AR): AR involves the overlay of digital information onto the real world. It is being used in operations management to improve training, maintenance, and troubleshooting. AR can help to reduce errors, improve efficiency, and reduce the need for physical prototypes.
Topic (7)-Sustainability in Operations
Definition of sustainability and its importance in Operations Management
Sustainability refers to the ability to meet the needs of the present without compromising the ability of future generations to meet their own needs. In Operations Management, sustainability involves designing and implementing processes and systems that minimize the negative impact of business operations on the environment, society, and the economy.
Here are some key points to consider when discussing sustainability in Operations Management:
(1) Environmental sustainability: This aspect of sustainability focuses on reducing the negative impact of business operations on the environment. Operations Managers can adopt sustainable practices such as energy-efficient technologies, recycling programs, and waste reduction initiatives to minimize the use of natural resources and minimize waste.
(2) Social sustainability: Social sustainability refers to the impact of business operations on people and society. This includes factors such as working conditions, human rights, and social responsibility. Operations Managers can implement sustainable practices such as ethical sourcing, fair labor practices, and employee development programs to promote social sustainability.
(3) Economic sustainability: Economic sustainability involves designing business operations that are financially sustainable over the long term. This includes reducing costs through efficiency gains, increasing revenue through innovation, and investing in research and development.
(4) Triple bottom line: The triple bottom line is a framework that incorporates economic, social, and environmental sustainability. It involves evaluating business operations based on their impact on people, planet, and profit.
(5) Sustainable supply chains: Operations Managers can work with suppliers to develop sustainable supply chains that minimize the impact of business operations on the environment and society. This involves evaluating suppliers based on their sustainability practices, as well as developing partnerships that support shared sustainability goals.
(6) Green operations: Green operations refer to the implementation of sustainable practices in the production and delivery of goods and services. This includes the use of energy-efficient technologies, the reduction of waste, and the adoption of environmentally friendly products and packaging.
Overall, sustainability is becoming increasingly important in Operations Management as organizations seek to reduce their impact on the environment, promote social responsibility, and achieve long-term financial sustainability. By adopting sustainable practices, Operations Managers can create a more resilient and responsible business that benefits all stakeholders.
Examples of sustainable practices in Operations Management
Sustainability has become a crucial factor in Operations Management as businesses are looking to reduce their negative impact on the environment and society. In this context, businesses are adopting sustainable practices in their operations to balance the needs of the present and the future. Here are some examples of sustainable practices in Operations Management:
(1) Waste Reduction: Waste reduction is an essential sustainable practice in Operations Management. It involves minimizing waste produced by the manufacturing process, and reducing the amount of waste sent to landfills. One of the ways to achieve this is through Lean Management, which focuses on reducing non-value added activities and streamlining processes. The use of biodegradable or recyclable packaging materials is another way to reduce waste.
(2) Renewable Energy: The use of renewable energy sources such as solar, wind, and hydro power can help reduce the carbon footprint of a business. In Operations Management, the installation of solar panels or wind turbines in manufacturing facilities is an effective way to reduce reliance on fossil fuels. The use of energy-efficient lighting and HVAC systems can also help reduce energy consumption.
(3) Sustainable Sourcing: Sustainable sourcing is a practice where businesses procure raw materials or goods from suppliers who meet certain environmental, social, and economic criteria. In Operations Management, sustainable sourcing involves selecting suppliers who have a proven track record of sustainable practices. For example, a company may prefer to source raw materials from suppliers who use organic farming practices or from suppliers who use renewable energy sources in their production processes.
(4) Green Logistics: Green logistics is a practice that involves the use of eco-friendly transportation methods and reducing the environmental impact of transportation. In Operations Management, businesses are adopting green logistics practices by using fuel-efficient transportation vehicles, optimizing routes to reduce the distance traveled, and utilizing intermodal transportation options.
(5) Circular Economy: The circular economy is an economic model that aims to minimize waste and maximize the use of resources. In Operations Management, businesses are adopting circular economy practices by reducing waste, reusing materials, and recycling products. For example, a company may adopt a closed-loop system where products are recycled or repurposed after use, rather than being discarded.
In conclusion, the adoption of sustainable practices in Operations Management can lead to various benefits for businesses, such as reduced costs, improved brand reputation, and enhanced customer loyalty. It is important for businesses to prioritize sustainability in their operations to achieve a balance between economic, social, and environmental factors.
Challenges and benefits of implementing sustainable practices in Operations Management
Implementing sustainable practices in operations management can be challenging, but it can also provide a range of benefits to businesses. Some of the key challenges and benefits of implementing sustainable practices are:
Challenges:
(1) Resistance to change: Implementing sustainable practices often requires changes in business processes, which can face resistance from employees who are used to established procedures.
(2) High initial investment costs: Adopting sustainable practices often requires investments in new technologies, equipment, and training, which can be expensive for businesses.
(3) Limited availability of sustainable resources: Sustainable resources can be scarce or difficult to obtain, which can make it challenging to source materials for production.
(4) Complex regulatory requirements: There may be complex regulations governing sustainable practices, which can be difficult for businesses to navigate and comply with.
(5) Limited consumer demand: Some sustainable products or services may have limited demand from consumers, which can limit the potential benefits of sustainability efforts.
Benefits:
(1) Reduced costs: Implementing sustainable practices can help reduce costs over time by improving resource efficiency, reducing waste and reducing energy consumption.
(2) Enhanced reputation and brand value: Sustainability initiatives can improve a company’s reputation and brand value, making it more attractive to customers, investors, and employees.
(3) Improved employee engagement and retention: Employees are often more engaged and motivated to work for companies that demonstrate a commitment to sustainability.
(4) Improved stakeholder relations: Sustainable practices can help build trust with stakeholders such as suppliers, customers, and local communities.
(5) Increased competitiveness: Sustainability practices can help businesses stand out from competitors and create a unique selling point.
Topic (8)-Ecological Considerations by Manufacturing and Services Firms
Overview of the impact of manufacturing and services on the environment
Manufacturing and services can have a significant impact on the environment, both in terms of resource consumption and waste generation. Here is an overview of the impact of manufacturing and services on the environment:
(1) Resource consumption: Manufacturing and services consume significant amounts of natural resources, including water, energy, and raw materials. For example, the production of goods requires large amounts of energy, such as electricity and fuel, which are often obtained from non-renewable sources. Services, such as transportation, also require energy and resources, which contribute to the depletion of natural resources.
(2) Waste generation: Manufacturing and services can generate a significant amount of waste, which can include both hazardous and non-hazardous waste. Hazardous waste, such as chemicals and electronic waste, can pose a significant threat to human health and the environment if not managed properly. Non-hazardous waste, such as paper and plastic, can also have a negative impact on the environment if not disposed of properly.
(3) Pollution: Manufacturing and services can contribute to pollution, including air and water pollution. For example, manufacturing plants can emit harmful pollutants into the air, such as carbon dioxide, sulfur dioxide, and nitrogen oxides, which can contribute to climate change and air pollution. Services, such as transportation, can also contribute to air pollution, particularly in urban areas.
(4) Land use: Manufacturing and services can also have an impact on land use. For example, the construction of manufacturing plants and service facilities can result in the loss of natural habitats and the displacement of wildlife. The extraction of raw materials can also have an impact on land use, particularly if it involves deforestation or the destruction of natural habitats.
(5) Climate change: Manufacturing and services are significant contributors to climate change, particularly through the emission of greenhouse gases. The production of goods and services requires significant amounts of energy, which is often obtained from non-renewable sources, such as fossil fuels. The use of energy from these sources releases carbon dioxide and other greenhouse gases into the atmosphere, which contributes to climate change.
Examples of environmentally-friendly practices in manufacturing and services
Examples of environmentally-friendly practices in manufacturing and services:
(1) Recycling: Recycling is a process of reusing waste materials instead of discarding them as trash. It helps to reduce the waste that goes to landfills and conserves natural resources such as timber, water, and minerals. Many manufacturers and service providers have implemented recycling programs to reduce their environmental impact.
(2) Reduced packaging: Packaging materials such as plastic and cardboard can contribute to environmental pollution. Many manufacturers have started using minimal packaging, reusable packaging, or biodegradable packaging to reduce their impact on the environment. Additionally, some companies are using innovative packaging materials made from sustainable materials such as bamboo or recycled plastic.
(3) Green buildings: Green buildings are designed to be environmentally friendly and sustainable. They are designed to use less energy, produce less waste, and reduce the environmental impact of the building. Many service providers such as hotels, restaurants, and offices have started to implement green building practices to reduce their impact on the environment.
(4) Energy-efficient lighting: Many manufacturers and service providers have started using energy-efficient lighting such as LEDs (light-emitting diodes) to reduce their energy consumption. LEDs use less energy than traditional lighting and have a longer lifespan, reducing waste and energy usage over time.
(5) Green transportation: Many service providers such as hotels and restaurants are implementing green transportation programs to reduce their environmental impact. This includes using hybrid or electric vehicles, offering public transportation or bike rental programs, and encouraging employees to carpool.
(6) Sustainable sourcing: Sustainable sourcing is the practice of using environmentally friendly materials and products in manufacturing and services. Many manufacturers and service providers have started to implement sustainable sourcing programs to reduce their impact on the environment. This includes using organic or recycled materials, sourcing materials locally to reduce transportation, and implementing fair labor practices.
(7) Reduced water usage: Many service providers such as hotels and restaurants are implementing programs to reduce water usage. This includes using low-flow showerheads and toilets, implementing water conservation programs for laundry and landscaping, and encouraging guests to reuse towels and linens.
(8) Renewable energy: Renewable energy sources such as solar, wind, and hydro power are becoming increasingly popular for manufacturing and services. Many companies are implementing renewable energy systems to reduce their dependence on non-renewable energy sources such as fossil fuels.
Importance of considering ecological factors in Operations Management
Ecological factors refer to the environmental impact of business operations and the extent to which they are sustainable. In recent years, the importance of ecological factors in Operations Management has grown significantly. It is increasingly recognized that businesses must take responsibility for their impact on the environment and adopt sustainable practices in order to protect natural resources for future generations.
The importance of considering ecological factors in Operations Management can be explained in the following ways:
(1) Environmental Responsibility: Businesses have a responsibility to minimize their impact on the environment. They must consider the ecological factors in their operations and take steps to reduce their carbon footprint and resource consumption.
(2) Competitive Advantage: Adopting sustainable practices can provide businesses with a competitive advantage. Consumers are increasingly concerned about the environmental impact of the products and services they use, and are more likely to choose companies that have a positive environmental record.
(3) Cost Reduction: Sustainable practices can also lead to cost reductions for businesses. For example, reducing waste and energy consumption can lead to lower costs for raw materials, transportation, and utility bills.
(4) Legal Requirements: Governments around the world are introducing legislation to regulate the impact of businesses on the environment. Compliance with these regulations is not only a legal requirement but also has an impact on the company’s reputation.
(5) Brand Image: The ecological impact of business operations can affect a company’s brand image. Companies with poor environmental records are likely to face negative publicity and damage to their reputation.